When there is a need for a vacuum gripping system that offers flexibility, integration and diagnostics, manufacturers of anthropomorphic robots and palletizing systems for packaging rely on Octopus by Vuototecnica, capable of handling items of all shapes and sizes.
Octopus is perfect, for example, when it comes to working in close contact with operators and for very light loads (for a maximum of ten kilos), as in the case of CO-BOT collaborative robots.
It is possible to handle bags with loose products, small objects, even with uneven surfaces, and many other details, without having to change the entire gripping system every time. All you have to do is remove the suction plate and replace it with another one.
The operating principle of Octopus gripping systems is based on the vacuum differential that is created inside their suction box, when the vacuum generator’s flow rate is greater than the amount of air sucked through the calibrated holes on the gripping plate.
The suction plates are interchangeable; it is possible to replace a suction plate with microholes covered with spongy rubber with a plate equipped with self-closing valves, according to the application.
The self-excluding valves of Vuototecnica Octopus system have the exclusive prerogative of being able to operate correctly in all positions of the suction plate with respect to the object to be picked up.
The spongy rubber is self-adhesive, easily replaceable and made with a special compound that allows gripping on irregular and rough surfaces and maintains elasticity even after countless cycles.
Alternatively, the Octopus gripping surface can be equipped with bellows suction cups that compensate for accentuated flatness errors. They are recommended, for example, for gripping deformable cardboard boxes and shrink-wrapped bundles of products.
Bellows suction cups are available in oil-resistant rubber, natural para rubber, silicone and, upon request, in special compounds.
Everything can be easily disassembled and inspected, even by non-specialized personnel.
The micro-holes of the suction plates are self-cleaning; the dust and dirt that pass through them do not settle and the suction section remains unchanged. A filtering disc made of stainless steel net retains dust. The impalpable dust, which the filtering disc does not retain, is sucked in and expelled by the vacuum generator.
The Octopus are also equipped with additional standard connections for control instruments and for the compressed air counter-blow for faster discharge of the lifted load.
For further customization, Vuototecnica can supply custom Octopus gripping heads, made with a 3D printer. A made-to-measure solution to meet every handling need, without problems of shape or material.
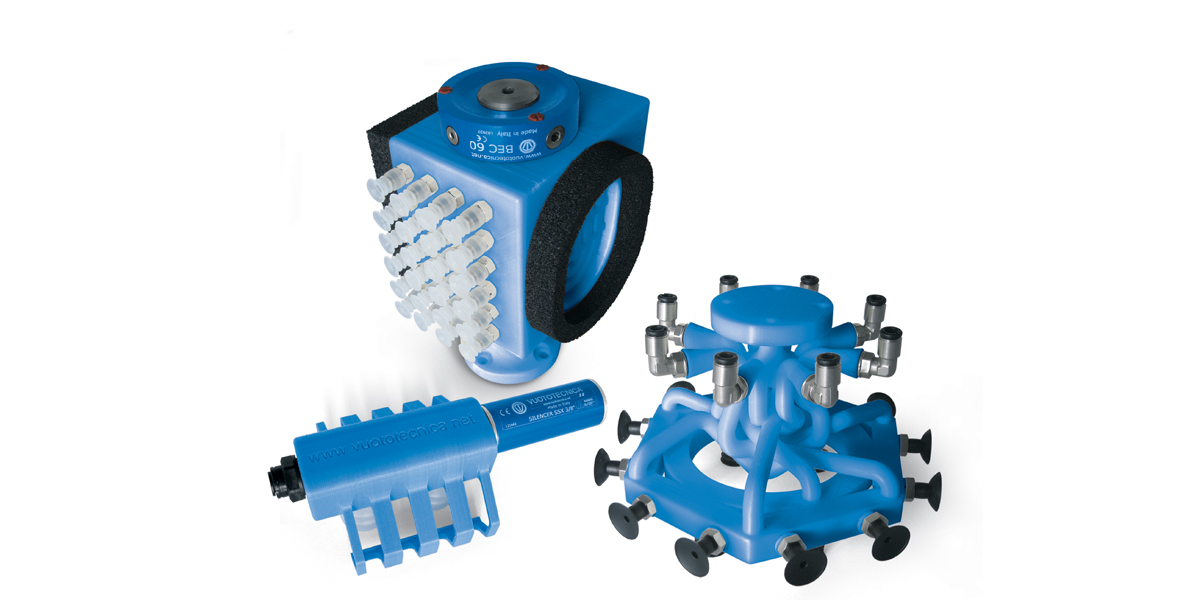
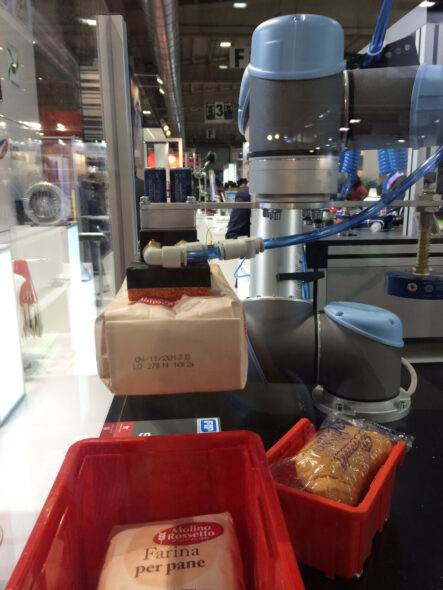
The heads are built ad hoc, in ABS, they are lighter as well as resistant, and gripping problems can be treated case by case, following the shape of the object.
The printer used to make the heads, installed at Vuototecnica’s technical office, uses FDM technology. Thanks to this additive manufacturing process, it is possible to respond in a very short time to the needs of customers: suction cup gripping hands made in just a few working days, even faster than the standard method with chip removal on CNC machines. Moreover, the design imagination knows no limits.
What’s more, the 3D gripper heads already have the vacuum source integrated. A plus for anthropomorphic robots and flexible pickers.
Read more: www.vuototecnica.net