Microplastics, tiny fragments of plastic smaller than 5 millimetres, represent one of the greatest environmental challenges of our time. These invisible pollutants are now found everywhere: in the oceans, rivers, soil and even in the air we breathe. But how do they spread and what solutions can we adopt to tackle the problem of plastic waste in general?
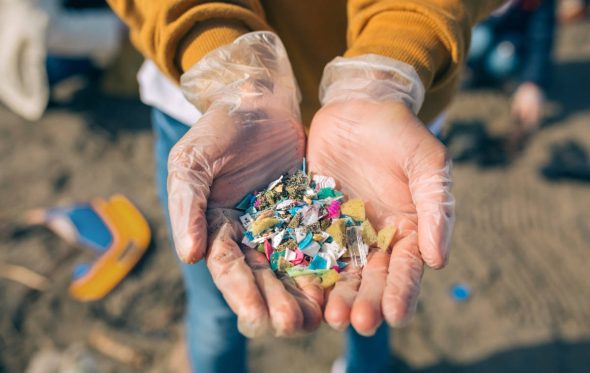
One of the answers may lie in vacuum conveying systems for recycling microplastics.
Vuototecnica’s CX vacuum conveyors can now help to pneumatically vacuum and transport plastic chips.
Powered by compressed air, they exploit the Coanda effect to suck in and convey ambient air like true flow multipliers: from one litre of compressed air consumed, almost 4 litres of air can be sucked in and conveyed through the main section of the aluminium body.
They have no moving parts, generate no heat in their operation and are therefore perfect even in working environments subject to fire or deflagration hazards.
They can be useful for transporting different types of materials over long distances: pellets and powders with a considerable height difference, for example.
Very easy to maintain, they are also available in stainless steel for transporting abrasive materials.
The most obvious advantage is that several CX conveyor systems mounted at regular distances of 3-5 metres from each other, on the same conveyor line; they would allow large quantities of plastic to be moved in a short time, minimising the risk of dispersion, and via a simple circuit of pneumatic air supply valves.
Furthermore, today’s proportional compressed air valve technology enables functional and highly consumption-efficient application scenarios.
Read more: www.vuototecnica.net.