To reduce global warming, there was much talk (and much was done) in recent years about increasing energy efficiency. In this regard, vacuum insulation panel technology was developed with very low thermal conductivity values, and can be used in a large number of applications.
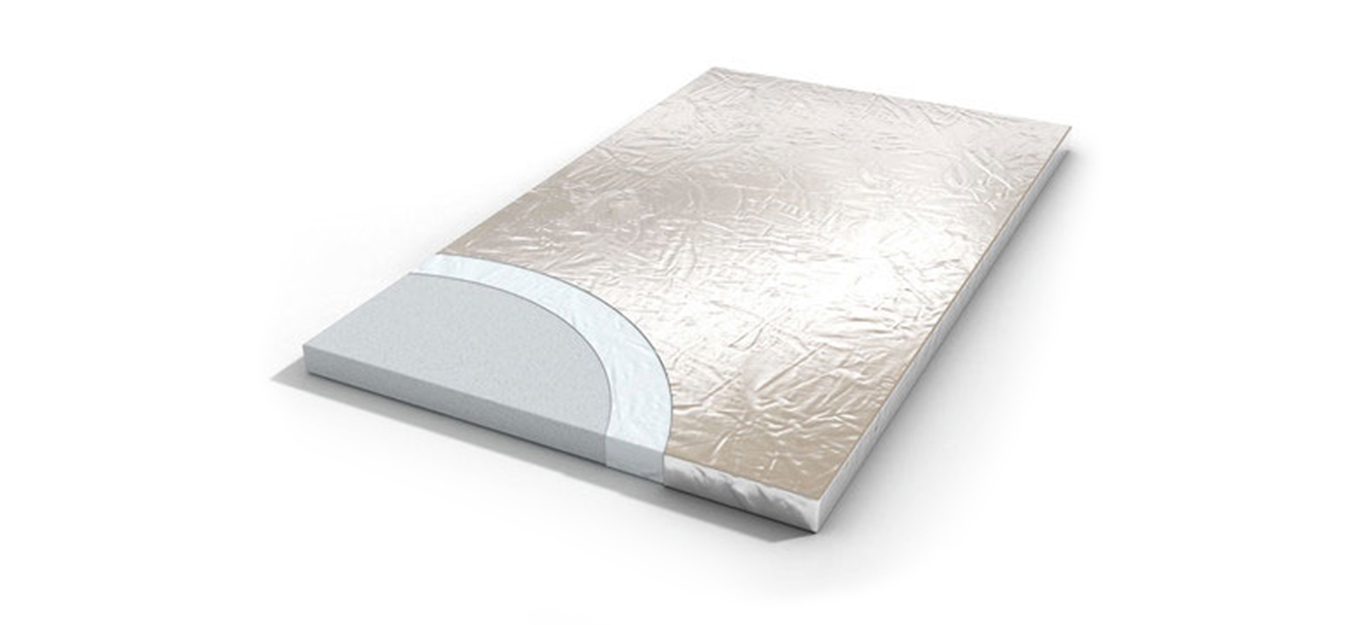
These panels have an efficiency up to 8 times higher than that of classic insulating materials and a smaller footprint (which often translates into economic advantages in addition to space).
They are already used in many applications, from refrigerators to domestic freezers, from vending machines to refrigerated/insulated transport (with a reduction of 10-30% on energy consumption), up to the building industry (both for energy requalification interventions and in new energy efficient buildings).
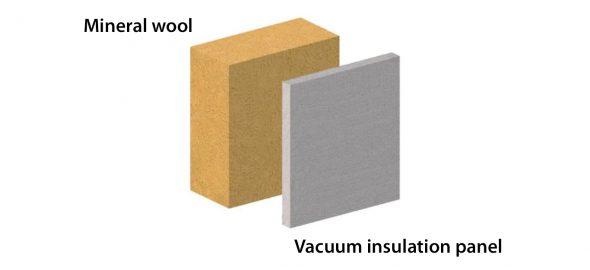
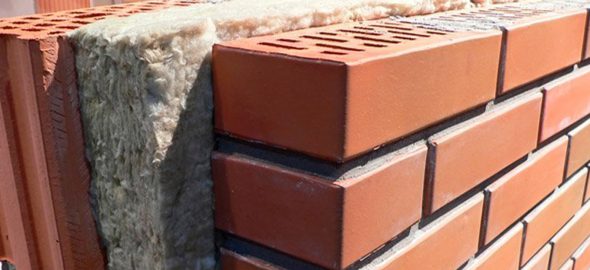
They were also implemented on biomedical and laboratory freezers that must necessarily reach very low temperatures (from -30 to -100 degrees) to store biological samples, vaccines and thermolabile drugs.
The vacuum insulating panels are vegetable matrix, mineral-based (microporous silicic acid) powdered pressed and placed in an aluminium vacuum casing and are deprived of air inside them.
It is a solution that can still show its best features and that, with the improvement of production techniques, is proving to be more and more performing.
For example, the vacuum in the panel must be maintained at an appropriate level throughout the life of the device, which can vary from a few months to several years.
Vuototecnica’s professionals have been vacuum specialists for half a century and they show enthusiasm for all applications related to energy saving and green economy.
To learn more about this application and to understand how to create vacuum in the most suitable way according to the application, you can visit the website www.vuototecnica.net